Deforestation unbalances ecosystems, erodes biodiversity and depletes carbon sinks. In the current year, forest fires and accelerating destruction of the rainforest in Brazil have prompted worldwide alarm and made us all a bit more conscious of the forests of our planet.
Instrument building is an extremely marginal business compared with many other industries that use wood as their raw material, not to speak of agriculture. Yet many instruments are made of wood, and the wood has to come from somewhere. It would be odd if no thought at all were to be given to the origin of raw materials in the world of music.
Classical instruments represent the utmost in refined craftsmanship. Their purpose is to produce an aesthetically pleasing sound, and they are rarely even thought of in terms of being material artefacts with physical properties – the properties of wood.
There are numerous requirements for the wood to be used in instruments, and different kinds of materials are needed for different parts of an instrument. For example, fingerboards require a very hard yet workable type of wood, typically a tropical hardwood. Also, different kinds of wood resonate in different ways.
Endangered materials
Maija Lampela has given a lot of thought to the woodiness of instruments. She is a viol player and a bog researcher who completed a doctorate on the restoration of tropical swamps in December 2018. Also in 2018, she graduated with a Master of Music degree from the Sibelius Academy. Tropical wood is a subject dear to her, and she takes a serious interest in how instrument building may affect forests of various kinds.
Guitar makers occupy a key position in this consideration. Acoustic and electric guitars are among the most widely selling instruments in the world, and guitars traditionally incorporate exotic kinds of wood that have now become endangered.
“The largest producers of tropical wood are Indonesia and Brazil,” says Lampela, who collected the material for her dissertation in Indonesia. “There’s certification, of course, but oversight is not always a simple matter, and you cannot always trust that a particular grade of wood has been sustainably harvested even if it claims to be.”
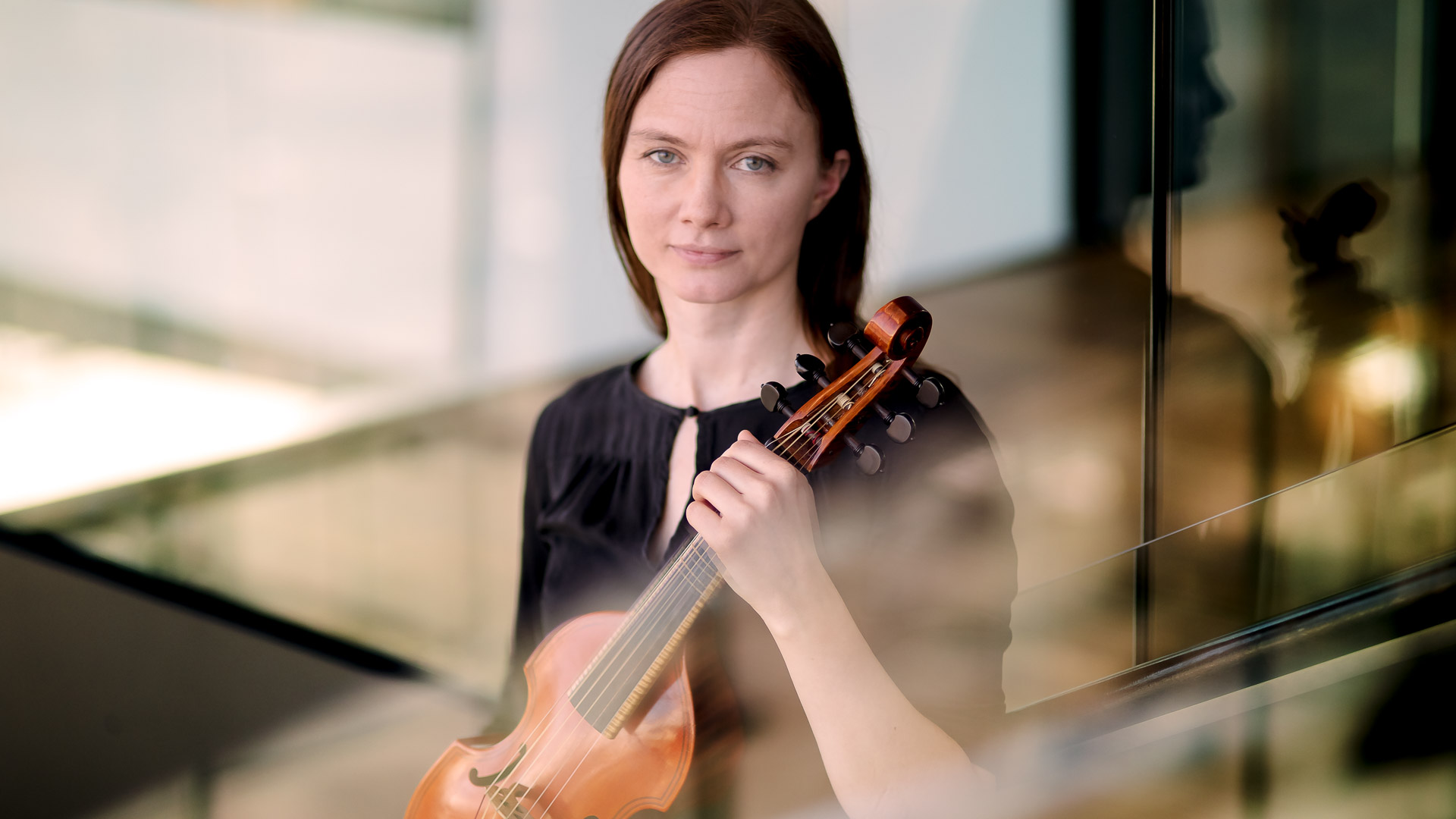
Photo: Jaakko Jaskari
There is no mention of sustainability on the websites of the world’s largest guitar manufacturers such as Gibson or Guild. By contrast, Taylor of California has introduced responsibility as part of its brand and prominently publicises its project in Cameroon to produce sustainable ebony.
Lampela notes that while the volume of instrument building is tiny in the big picture, many instruments traditionally require materials that are now endangered or unsustainable. As an example, piano keys and detail work on bows used to be made of ivory, but this was replaced years ago with synthetic materials – or with mammoth ivory found in melting permafrost.
For a long time now, the most coveted type of wood among guitar builders has been Brazilian rosewood (Dalbergia nigra), which in 1991 was listed in the highest protection category in CITES (the Convention on International Trade in Endangered Species) because of overuse. At the moment, it is only legal to harvest Brazilian rosewood from the stumps of trees felled before 1991. However, this regulation is difficult to enforce. In rural areas, people may secretly take down protected trees in order to make a living, and it may be practically impossible to find out the origin of any particular quantity of wood.
Locally sourced wood
Most of the wood for classical string instruments is traditionally found close to home: alpine spruce for the top plate, maple for the ribs and plates. Related tree species are also found in China, which is now a source for plenty of affordable string instruments of good quality.
Maija Lampela has considered whether it would be possible to source wood for instruments in Finland. “The quality requirements are really strict, though, and the rapid-growth forests of Finland do not really produce spruce trees that are thick enough, even enough in structure and free of branches.
When Lampela recently acquired a new bass viol from the south of France, she found that the builder had used materials sourced as locally as possible: pearwood and boxwood. “Instrument builders may also have stashes of old wood acquired from builders long ago and dating back heaven knows how many decades. This is because the wood used for instruments needs to be really dry,” says Lampela.
The ecological sticking point in string instruments is the bow, which requires a very hard yet flexible wood. Such stuff is only found in rainforests. Current bows mainly use Pernambuco wood, which is an endangered species. “Carbon fibre is OK for practice, but there’s no substitute for a natural material. What options are there available for bows? It’s a real problem,” says Lampela.
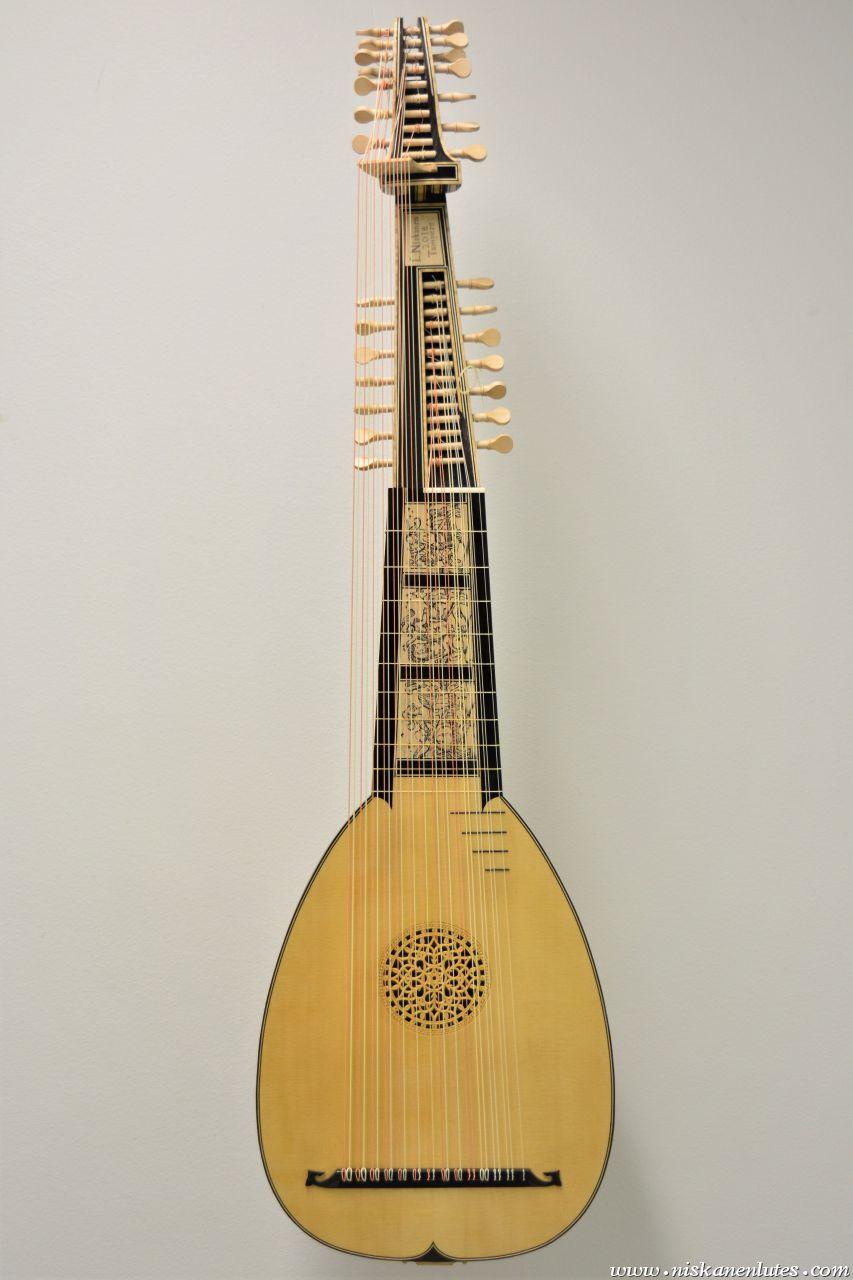
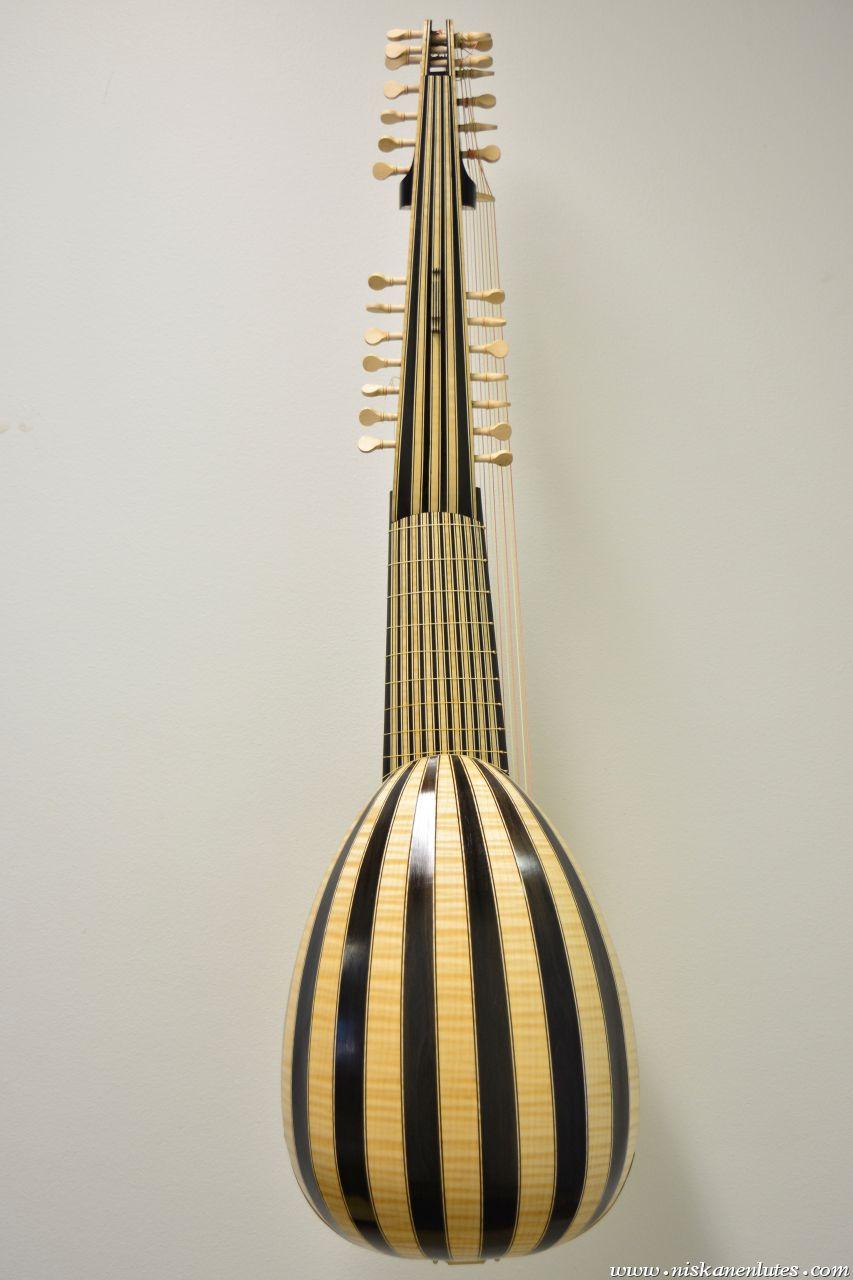
New options
Alternative materials – types of wood not previously used as well as synthetic materials – are needed to replace endangered types of wood.
Lauri Niskanen has been building historical stringed instruments in Tampere for almost eight years and has customers around the world. His lutes and theorbos contain woods that seem very familiar, such as curly birch (sourced from Kajaani), roasted flame maple, pearwood and alpine spruce. He does use exotic woods as well: padauk from Pterocarpus trees that grow in Africa and Southeast Asia, and sapele from Africa. Niskanen mentions that he has experimented with replacing ebony with Blackwood Tek, a product made of New Zealand pine treated and stained to resemble ebony. Guitar makers are already familiar with this material.
“I’ve also dyed walnut myself using vinegar and steel wool, and the end result was a pretty nice black and flexible wood,” says Niskanen.
The need for a new approach to materials has penetrated the guitar industry. The new wave is represented by operators such as Madinter, an ecologically oriented online shop for music instrument materials based in Spain. They have promoted Blackwood Tek, among other things.
Material innovations have been made in Finland too, fostered by awareness of the endangered nature of traditional instrument materials and by a demand for more sustainable alternatives. Partones from Salla in Lapland, founded by Kristiina Aatsinki and Armin Seebass, has developed alternatives for ivory and ebony and are working on others.
Flaxwood, created in North Karelia, is a wood fibre composite intended for electric guitars. “The decision to use wood fibre composite in guitars was not based solely on the material being an ecological choice. The sound properties of the material are a major factor in Flaxwood guitars: WFC is highly resonating, stable and dynamic,” according to the Flaxwood website. The company continues to develop instruments.
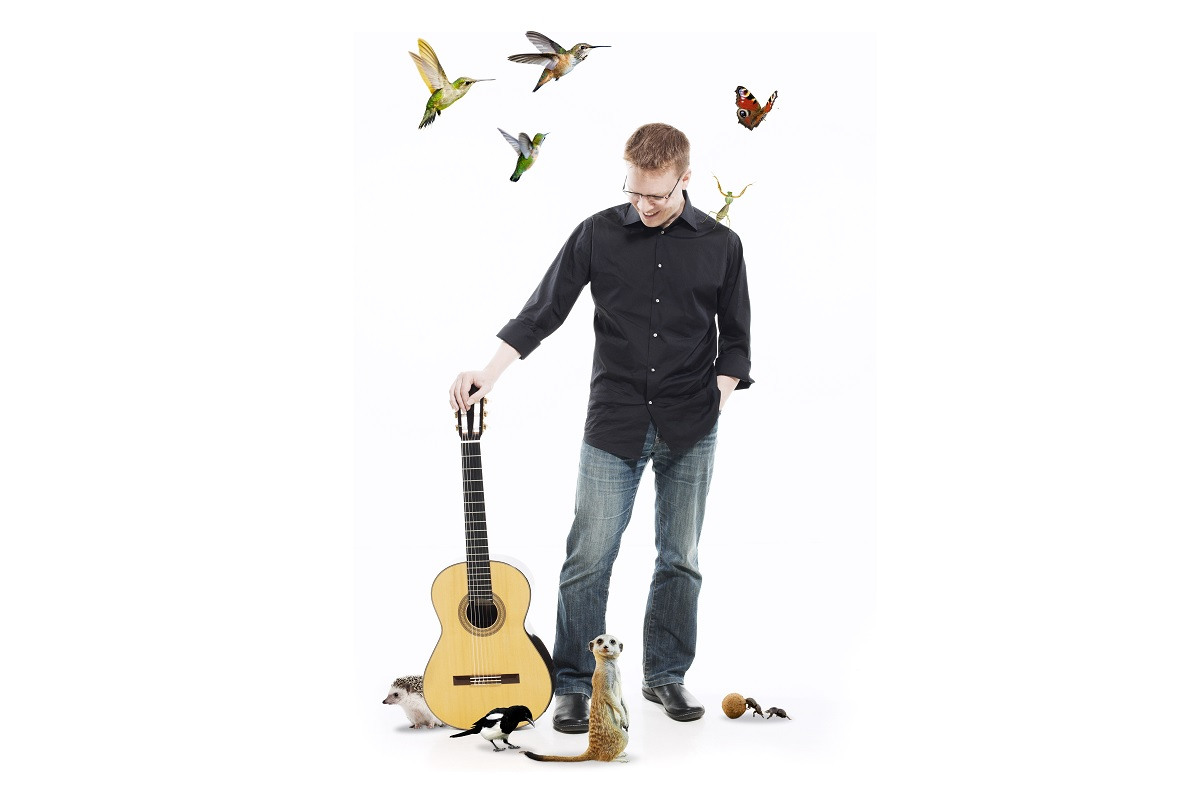
Photo: Marek Sabogal
Open hearts, open minds
“Each and every experiment with alternative materials is welcome. We need new ideas and solutions, because instrument builders are gradually running out of their stocks of wood,” says guitar player Petri Kumela. He is very familiar with the materials in his instruments and their origins, and ecological sustainability is an important factor for him when selecting an instrument, “just as it is in buying anything else”.
“For me, when I select an instrument, its materials must meet certain ecological standards, but beyond that the choice is down to other properties, although the materials used of course affect those too,” says Kumela. “I’ve been working with an Italian guitar maker for many years, and we’ve been able to talk about these things over time and think about the structure of the guitar in ways that facilitates a desirable outcome.”
Maija Lampela feels that wind players typically have a more flexible attitude to their instruments than string players. Wind instruments have changed a lot over the centuries, and experimenting with carbon fibre and synthetic materials to replace rare woods in them is nothing new. Lampela notes that people have a lot of emotional investment in particular materials.
“There are many conceptions about which materials provide the best sound. String instruments have remained unchanged for centuries, and there is a lot of mysticism around them. Under those circumstances, it may be more difficult to gain approval for new materials. Yet people are the ones making the instruments and playing them, not the wood,” says Lampela.
Translation: Jaakko Mäntyjärvi
Featured photo: A violin with a fingerboard made of Parbony, Partones's ebony replacement.